Instructed by experts from the AIAA Pressure Gain Combustion Technical Committee
ü This 16-Hour on-demand course provides an overview of the unique aspects of PGC, beginning with a historic perspective of PGC and include thermodynamic theory comparing PGC to other relevant power cycles, and followed by an overview of several major classes of PGC such as Pulse Combustion, Wave Rotor Combustion Engines (WRCE), Pulse Detonation Engine (PDE), and Rotating Detonation Engines (RDE).
OVERVIEW
Unlike conventional isobaric combustion, pressure gain combustion (PGC) is focused on technologies that are able to increase the pressure of the working fluid through the combustion process without the need for additional mechanical compression. PGC can be achieved with either deflagration or detonation although the mechanism for pressure gain would be different depending on the method of combustion. Regardless of the approach, PGC offers greater work availability compared to isobaric combustion, but it has unique challenges. As a result of the potential improvement in cycle efficiency, as well as advances in computational and experimental methods, there has been a growing interest in PGC for applications in aerospace propulsion and power generation.
This course provides an overview of the unique aspects of PGC. The course begins with a historic perspective of PGC and include thermodynamic theory comparing PGC to other relevant power cycles. This is followed by an overview of several major classes of PGC such as Pulse Combustion, Wave Rotor Combustion Engines (WRCE), Pulse Detonation Engine (PDE), and Rotating Detonation Engines (RDE). As PGC research has its own unique challenges, the course offers a review of relevant and state-of-the-art computational and experiments methods that are utilized in both fundamental and more applied studies. The course includes a discussion of systems integration along with lessons learned from some demonstrated applications. Government-funded programs have been critical and the course includes an overview of the various programs and potential roadmaps for helping to advance the technology forward. Instructors from this course come from various reaches of technology development including fundamental research, program direction, and industry.
(Course recorded live in 2023)
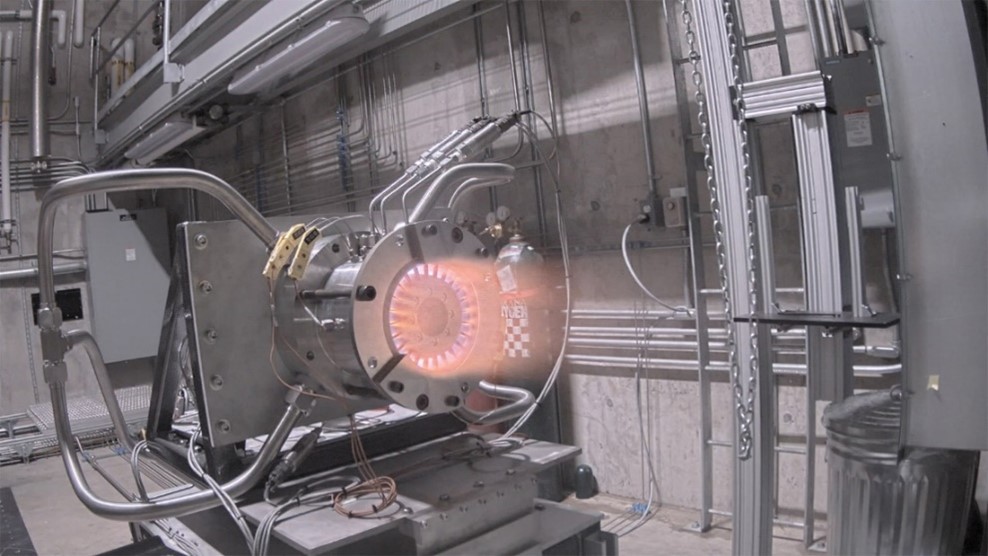
LEARNING OBJECTIVES:
- A historical context in the development of PGC systems
- Qualitative background of the fundamental physics pertinent to PGC, including low-order physical and thermodynamic modeling, highlighting the difference from the Brayton cycle.
- An understanding of different PGC systems and their pros and cons
- An understanding of the integration of PGC systems to other components for aerospace propulsion and for power production
- An awareness of the challenges involved in developing PGC technologies
MATERIALS:
- Introduction / Historical Review
- Fundamentals of Gas Dynamics of Deflagrations (CVC)
- Fundamentals of Gas Dynamics of Detonations (Detonations)
- Cycle analysis, Ideal & Real Cycles: Benefits of Pressure Gain, Brayton, Humphrey and Atkinson
- Pressure Gain Combustion Applications: Pure propulsion-Rockets and missiles, Hybrid Propulsion - gas turbines – powergen & aviation
- Pressure Gain Concept & Device: Wave Rotor Combustion Engines
- Pressure Gain Concept & Device: Resonant Pulse Combustion Engines
- Pressure Gain Concept & Device: Pulsed Detonation Engines
- Rotating Detonation Engines: Concepts and Applications
- Fundamentals of RDE: Cycle Considerations & Gas Dynamics
- RDE Experiments
- RDE Computations
- RDE Applications
- Summary and Roadmap, Q&A
Lead Instructor: Dr. Frank Lu
Dr. Lu is a Professor of Mechanical and Aerospace Engineering at the UT Arlington. He has worked in an academic setting in experimental aerodynamics and aerospace propulsion for over 30 years, as well as consulted in these areas. His primary expertise is in shock/boundary-layer interactions and in applications of detonations for aerospace propulsion and in aerodynamics test facilities. He co-edited an AIAA Progress Series volume entitled Advanced Hypersonic Test Facilities, which was well received by the aero-test community. He is lead author of a proposed text on hypersonic vehicle design that will be published in 2023. Dr. Lu earned his degrees from Cambridge, Princeton, and Penn State. He is a Life Fellow of AIAA, a Distinguished Life Fellow of the International Shock Wave Institute, a Fellow of ASME and RAeS, and a Guggenheim Fellow. He is active in AIAA activities, having served as Editor-in-Chief of the Progress Series and as Vice President of Publications amongst various roles.
Dr. Razi Nalim is Executive Associate Dean for Research & Global Initiatives for the Purdue School of Engineering & Technology in Indianapolis. He has led industry-university research consortia to develop pressure-gain combustors for powerplants and jet engines, emissions controls for large-bore gas engines, and autonomous and electrified vehicle technologies. His research for NASA and Rolls-Royce led to the first US demonstration of a wave rotor combustor at Purdue University’s Zucrow Labs. He has been active in the Gas Turbine and Pressure Gain Combustion technical committees of AIAA, organizing technical sessions and teaching short courses. He conducts workshops in project-based active learning in STEM education and has received awards for undergraduate research mentoring and teaching. He has published widely, received 7 patents, and was supported by over $12 million in research and training grants from industry and government.
Dr.
Daniel E. Paxson is an aerospace research engineer in the NASA John
H. Glenn Research Center’s Research and Engineering Directorate. He earned his
B.E. degree in mechanical engineering from Vanderbilt University and his M.S.
and Ph.D. degrees at Rensselaer Polytechnic Institute. Since graduation, Dan has been at NASA
conducting both experimental and analytical research in the areas of unsteady
fluid mechanics, gasdynamic propulsion and power systems, and pressure gain
combustion. He has developed simulation,
design, and optimization software, and designed or assisted the design and
operation of experiments for wave rotor technologies, active combustion
instability control, high speed valve systems, pulsed ejectors, resonant pulsed
combustors, pulse detonation engines, and rotating detonation engines. He has
served numerous times as a subject matter expert in these areas for the U.S.
Departments of Defense and Energy. Dan
is an Associate Fellow of AIAA. He
serves on the AIAA High Speed Airbreathing Propulsion Technical Committee (TC),
and the AIAA Pressure Gain Combustion TC.
He is also a member of the JANNAF Pressure Gain Combustion Working
Group.
Dr.
Douglas Schwer
received his doctorate in Mechanical Engineering in 1999 and did a brief
post-doc at MIT before joining the Naval Research Laboratory in 2001. Since
2009 Dr. Schwer has been the lead investigator for numerical simulations of
rotating detonation engines at NRL, writing a suite of codes to examine
different aspects of RDEs, with numerical models and algorithms based on
previous work accomplished at NRL in pulsed detonation engines. He has studied several different aspects of
RDEs numerically from basic flow-field thermodynamics to dynamics found in full
rig simulations and has been an active participant of AIAA forums in pressure
gain combustion at all levels.
Mr. Jeff Stout has become one of the most experienced researchers of rotating detonation engine technology in the US over the last 12 years. He has acted as chief engineer, project engineer, lead designer, and experimentalist for many projects that featured an RDE as the core technology. These include: designing dozens of RDE engine sets with over 70 injectors, setting up offsite hot fire test at 12 different facilities, conducting 28 test campaigns and executing thousands of hot fire tests. Prior to his work with RDEs, he has also been the principal investigator, primary designer, and test engineer for over a dozen liquid rocket engine (LRE) technology development programs conducting over 800 hot fire tests in this field. His work with LREs emphasized developing combustion chambers and nozzles utilizing advanced ceramic matrix composite materials, many of them with integrated active cooling for high heat flux applications.
CONTACT: Please contact Lisa Le or Customer Service if you have any questions about the course or group discounts (for 5+ attendees).
Title | Credit(s) | |
---|---|---|
1 | ||
2 | ||
3 | ||
4 | ||
5 | ||
6 | ||
7 | ||
8 | ||
9 | ||
10 |