Instructed by Wenbin Yu, Professor of Aeronautics and Astronautics at Purdue University; Xin Liu, Assistant Professor of Industrial, Manufacturing, & Systems Engineering Department at UT Arlington.
ü From 5 August – 28 August 2020 (4 weeks, 8 Lectures, 20 Hours)
ü Every Wednesday and Friday at 1300-1530 Eastern Time (all sessions will be recorded and available for replay; course notes will be available for download; students will be able to launch computer codes online)
ü This introductory course focuses on the hands-on training and advanced online tools for multiscale modeling using SwiftComp
ü Course will also include illustrative application examples, practice exercises, and supplemental material to enhance the learning experience
ü All students will receive an AIAA Certificate of Completion at the end of the course
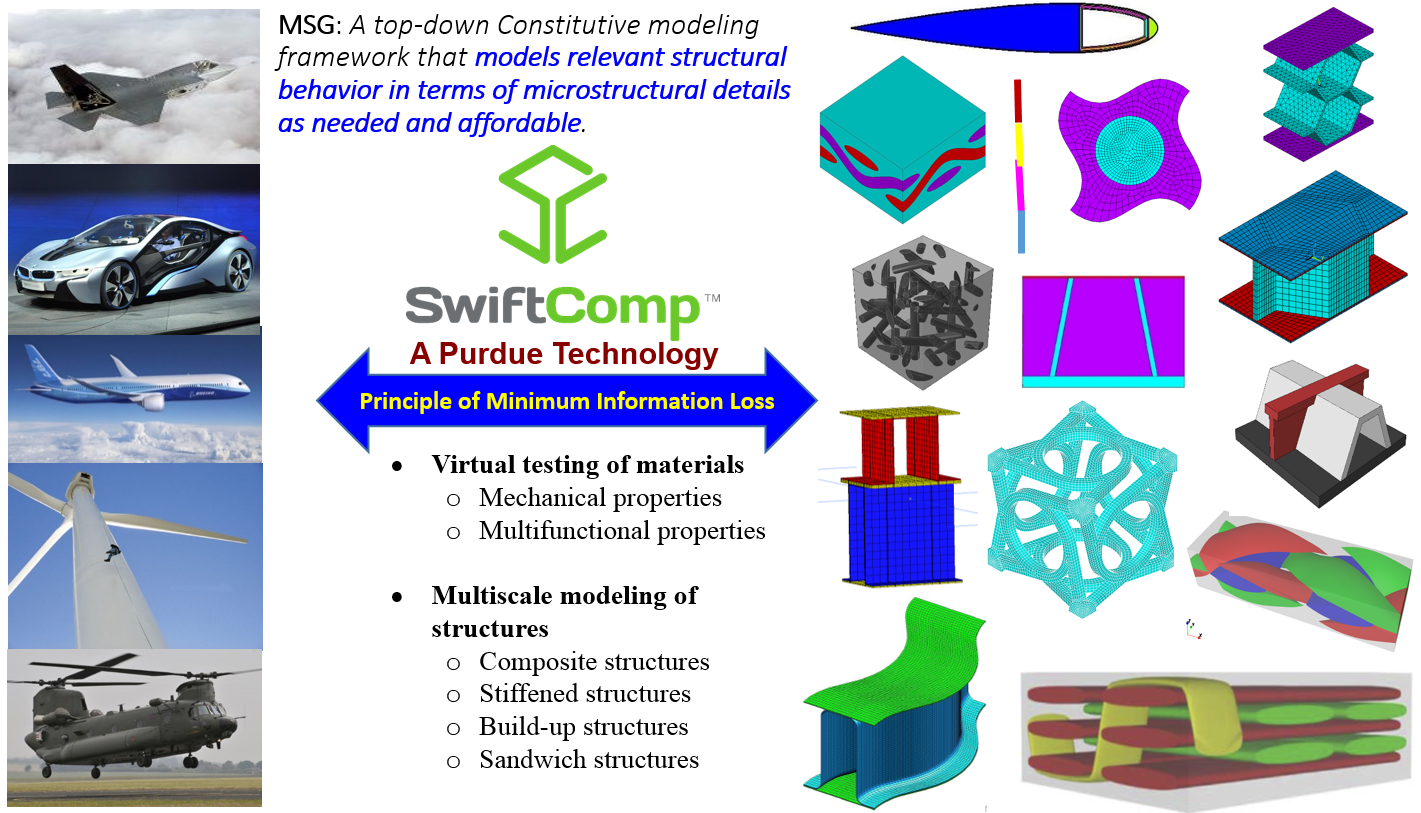
Overview
This course will introduce mechanics of structure genome (MSG) as a unified framework for multiscale modeling of composite structures and materials starting from fiber/matrix scale all the way to macroscopic structural scale. This course will emphasize skills of using MSG-based online software tools to perform simulation needed for design and analysis of various types of composite structures such as unidirectional (UD) fiber reinforced composites laminates, 2D and 3D textile composite structures, and honeycomb sandwich structures. This course will use several composites simulation tools on cdmHUB (https://cdmhub.org/) which will be freely accessible for registrants.
What You Will Learn
- Challenges associated with modeling of composite materials and structures.
- Basic ideas of multiscale modeling of composite materials and structures.
- Basic ideas of MSG and the advantages of MSG compared with other approaches for modeling composite structures and materials.
- How to use MSG for micromechanical analysis of composites: predict lamina constants and 3D properties of composite laminates, failure of various types of composite materials.
- How to use MSG for modeling thin composite structures as a plate: predict ABD matrices, in-plane and flexural properties of composite laminates, equivalent plate properties for honeycomb sandwich structures, failure of composite panels, etc.
- How to use MSG for modeling slender composite structures as a beam: predict equivalent beam problems for composite rotor blades, high-aspect ratio wings, deployable booms, failure of composite slender structures.
Key Course Topics
- State-of-the-art multiscale methods
- MSG and its companion online tools
- MSG-based micromechanics modeling of composites (e.g., UD composites, particle reinforced composites, and textile composites)
- MSG-based plate modeling of thin composite structures (e.g., UD laminates, woven laminates, and honeycomb sandwich structures)
- MSG-based beam modeling of slender composite structures (e.g., I beam, Box beam, tubes, and rotor blades, and other irregular sections)
- MSG-based failure analysis for typical composite structures and materials (e.g. UD laminates, woven composites, honeycomb sandwich structures)
Who Should Attend
This course is intended for structure engineers and researchers who need to perform stress and failure analysis for design and manufacturing of composite structures. It is also suitable for professors and graduate students who are interested in learning cutting edge tools for multiscale modeling and simulation of composite structures and materials. This online course aims a balanced focus of theoretical fundamentals and hands-on use of advanced computer codes for modeling of composite materials and structures. The students are assumed to have basic knowledge about mechanics of composite materials.
Course Fees (Sign-In to Register)
Non-Member Price: $1045 USD
AIAA Member Price: $845 USD
AIAA Student Member Price: $495 USD
Classroom hours / CEUs
20 classroom hours
2.0 CEUs
Detailed Outline:
Lecture 1 Fundamentals of composites modeling
1.1 Challenges for modeling and simulation of composite materials and structures
1.2 Typical modeling approaches for composite materials and structures
Lecture 2 Mechanics of structure genome
2.1 Introduction to the concept of structure gene (SG) and MSG
2.2 Applications and advantages of MSG
Lecture 3 Micromechanics modeling
3.1 Theoretical fundamentals of MSG-based micromechanics
3.2 Applications of Gmsh4SC to model typical composites: laminates, fiber reinforced composites, particle reinforced composites, etc.
3.3 Applications of TexGen4SC to model textile composites
3.4 Hands-on exercises
Lecture 4 Plate modeling of composite panels
4.1 Theoretical fundamentals of MSG-based plate modeling
4.2 Demo examples for computing equivalent plate properties (ABD matrices, in-plane and flexural properties)
4.3 Hands-on exercises
Lecture 5 Beam modeling of composite slender structures
5.1 Theoretical fundamentals of MSG-based plate modeling
5.2 Demo examples for computing equivalent beam properties (extension, bending, torsion stiffness, neutral axis, shear center, etc.) for composite blades, high aspect ratio wings, tubes, etc.
5.3 Hands-on exercises
Lecture 6 Failure analysis of composites
6.1 Theoretical fundamentals of MSG-based failure analysis of composites
6.2 Demo examples for predicting strength constants, strength ratio/failure index, and failure envelope
6.3 Hands-on exercises
Lecture 7 Thermoviscoelastic modeling of composites
7.1 Theoretical fundamentals of MSG-based thermoviscoelastic modeling of composites
7.2 Demo examples for computing CTEs, and other time-dependent and temperature-dependent properties
7.3 Hands-on exercises
Lecture 8 Multiscale design and analysis of aerospace structures
8.1 Basic guidelines for multiscale design and analysis of aerospace structures
8.2 Demo examples for multiscale design and analysis of typical aerospace structures including composite rotor blades, high aspect ratio wings, and deployable composite booms
8.3 Hands-on exercises
Instructors
Dr. Wenbin Yu is a Professor in the School of Aeronautics and Astronautics at Purdue University. He also serves as the Director for Composites Design and Manufacturing HUB (cdmHUB), the Associate Director for Composites Virtual Factory HUB (cvfHUB), and the CTO for AnalySwift LLC. His expertise is in micromechanics and structural mechanics with applications to composite/smart materials. He has authored/co-authored 200+ journal papers and refereed conference papers and developed seven computer codes which are being used by tens of thousands of researchers and engineers in government labs, universities, research institutes, and companies. His research has been funded by both federal agencies and private industry. He is an ASME Fellow and AIAA Associate Fellow. He is the current chair of AIAA materials TC and chair-elect for ASME aerospace division. He serves on the editorial board for four international journals and the Steering Committee of the annual ASME International Mechanical Engineering Congress and Exhibition.
Dr. Xin Liu is an Assistant Professor in the Industrial, Manufacturing, & Systems Engineering Department at the University of Texas at Arlington. He is also a member in the Institute for Predictive Performance Methodologies at the UTA Research Institute. His expertise is in data-driven multiscale modeling of composite materials and structures. He has authored/co-authored 20+ journal papers and refereed conference papers. He also developed three computer codes for multiscale modeling of composites. He received the American Society for Composites (ASC) Ph.D. Research Scholarship Award in 2018 and Purdue University Koerner Scholarship in 2017.
The course lectures will be delivered via Zoom. You can test your connection here: https://zoom.us/test
Access to the virtual classroom will be provided to registrants near to the course start date.
All sessions will be available on-demand within 1-2 days of the lecture. Once available, you can stream the replay video anytime, 24/7.
All slides will be available for download after each lecture. No part of these materials may be reproduced, distributed, or transmitted, unless for course participants. All rights reserved.
Between lectures and other time, the instructor will be available for answering technical questions and comments through a dedicated online discussion board on cdmHUB.
Cancellation Policy
A refund less a $100.00 cancellation fee will be assessed for all cancellations made in writing prior to 14 days before the start of the event. After that time, no refunds will be provided.
Contact
Please contact Jason Cole or Customer Service if you have any questions