Instructor: Don Edberg, Professor of Aerospace Engineering at Cal Poly Pomona & Adjunct Lecturer, Astronautical Engineering, University of Southern California (USC), Former Boeing Technical Fellow
Overview
This 24 Hour on-demand course (12 two-hour lectures) presents a coherent and comprehensive treatment of the fundamental principles involved with the interdisciplinary design of launch vehicles. It is recommended for anyone who is interested in a comprehensive introduction to all of the principles and aspects of launch vehicle design and development, including engineers of all types – systems, aerodynamics, controls, structures, dynamics, thermal analysis, propulsion, reliability, manufacturing, as well as researchers, mission designers, technical managers, and both undergraduate and graduate students. This course provides a survey of the material in the instructor’s AIAA textbook “Design of Rockets and Space Launch Vehicles” (2020), with additional materials on current topics such vehicle reusability and small launch vehicles.
Course held live in Spring 2021
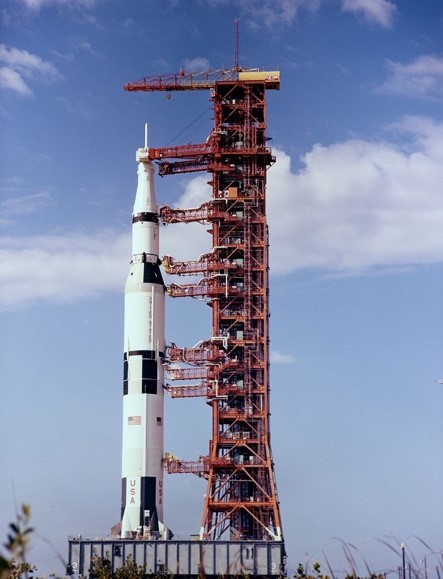
What You Will Learn
After an introduction, you will be the anatomy of a typical launch vehicle (LV) and its ascent into orbit. The step-by-step details of the design process are followed by listings of worldwide launch sites and a discussion of the space industry.
Subsequent lectures include a detailed technical history of LVs along with current and future LVs, an introduction to mission requirements which define LV performance, and orbit information. A comprehensive discussion of rocket propulsion is followed by a detailed lecture on rocket performance and staging analysis. Next comes a detailed discussion of powered flight and trajectory analysis, showing how to make a spreadsheet to numerically simulate a LV ascent, along with examples of ascent profiles from existing vehicles. The next lecture provides details on LV structures, construction, and materials.
Next, design begins in earnest. The inboard profile is laid out by computing the necessary propellant tank sizes, as well as connecting structures, selecting propulsion system, and determining mass properties. A lecture on loads calculates ground loads and loads that occur during flight through the atmosphere. These loads, along with pressurization, are used to calculate internal structural stresses and size wall thicknesses.
We then provide additional details of the launch environment, including vibration, shock, acoustic, and thermal effects. Another lecture presents the basics of stability/control and assesses the effects of instabilities that occur due to structural flexibility, propellant sloshing, and other phenomena.
After this, both traditional and modern manufacturing processes are shown, including both metallic and composite structures. Another lecture provides details on the necessary systems inside of LVs and their interfaces with the services on the launch pad. A lecture on testing surveys many testing methods used and discusses redundancy and reliability. Another lecture provides the details of different types of LV failures and best practices to avoid them, as well as information on flight termination systems. The course ends with a discussion of financial analysis of LVs, project management, and cost estimation.
- Technical history of launch vehicles (LVs)
- Current LVs and new developments
- Mission requirements and top-level performance analysis for LVs
- Velocity calculation including gravity, drag, and other losses
- Propulsion systems: liquid, solid, and hybrid. Engine cycles, system performance, critical parameters
- LV performance estimation including series & parallel staging, vehicle trade-off ratios
- Vehicle equations of motion with aerodynamic loads, including trajectory simulations; launch optimization including lofting and other techniques
- LV structure types and materials including aluminum, Al-Li, composites
- LV internal layouts, tank and vehicle sizing, and mass properties including center of mass and inertias
- Vehicle aerodynamics, ground and ascent loads including example Saturn V loads analysis
- LV stress calculations related to wind loads, internal pressurization, strength, and structural stability
- Vibration, shock, acoustic, and thermal environments
- Vehicle stability and control
- Instabilities including flexible body effects, Pogo, propellant sloshing; structural, and propulsion instabilities
- Manufacturing processes for both metallic and composite structures, vehicle assembly
- On-board LV systems including propellant delivery and conditioning, power, control, telemetry, and launch pad facilities, lightning protection, vehicle restraint systems
- Testing: wind tunnel, structural, vibration, acoustics, propulsion, and more
- A sampling of LV failures and lessons learned
- Reliability of LVs and range safety
- LV development and operations cost estimation
- [See Detailed Outline Below]
Audience: This course is intended for engineers of all types – aerodynamics, controls, structures, propulsion, reliability, manufacturing, systems, as well as researchers, mission designers, technical managers, and both undergraduate and graduate students, who want to enhance their understanding of the fundamental principles of the design and operation of space launch vehicles. This introductory course focuses on the basic physical concepts and mathematics utilized in the preliminary design and analysis of launch vehicles including many practical aspects not found elsewhere.
Course Materials: Over 1500(!) pages of high-quality course notes will be available for immediate download. Stream the 24+ hours of lecture video recordings anytime 24/7. No part of these materials may be reproduced, distributed, or transmitted, unless for course participants.
Classroom hours / CEUs: 24 classroom hours/ 2.4 CEUs. Receive an AIAA Certificate of Completion upon viewing of all of the lectures.
Course Fees (Sign-In to Register)
- Non-Member Price: $1,395
- AIAA Student Member Price: $695
Course Outline:
Lecture |
Subject |
1. |
(1)Launch vehicle (LV) introduction: anatomy of a LV, launch & ascent phases. Launch sites & space industry. Market & need for LVs. (2)Technical history of rocketry & LVs: early events, WWII, the Cold War, ICBMs. |
2. |
(2) History of LVs (cont.): moon race, space shuttle, oddities. Current & future LVs. (3) Requirements and missions. Orbits & trajectories: due east, direct orbits, polar, sun-synch, Molniya. Launch energy, launch azimuth angle calculation, launch windows, orbit injection & shutdown conditions. |
3. |
(4) Propulsion. Exhaust speed, mass flow, calculation of thrust & ∆v. Solid motors: grain, thrust profiles. Liquid engines: room-temp vs. cryogenic propellants. Hypergolics. Mixture ratios, performance, specific impulse. Engine thrust-to-weight ratio. Aerospike engines, hybrid rockets. |
4. |
(5) Launch vehicle parameters & performance. The three categories of LV mass. SSTO & benefits of staging. Four types of staging, including series & parallel. Optimal staging with losses. All hydrogen-fuel Saturn V? Propellant crossfeeding? LV design sensitivities: where is the best place to improve performance? |
5. |
(6) Powered flight through atmosphere. LV aerodynamics. Moving vehicle coordinate system, local horizon frame, launch site motion. Buoyancy! Gravity & drag loss. The gravity-turn trajectory. Other types of guidance. Numerical integration to trajectory analysis. |
6. |
(6 cont.) LV trajectory optimization: Newton & first optimization problem. Conflict between gravity & drag/thermal loads. Lofting. LV trajectory examples: Delta, Saturn, Shuttle, Ariane, others. (7) LV structure examples: Thor evolution to Delta, Saturns, Space Shuttle. Payload accommodations, fairing, attach fitting. Structure types: skin & stringer, sandwich, isogrid/orthogrid. Materials: metallics (Al, Al-Li, Ti, Steel) & composites (Gr-epoxy, fiberglass, aramid). Property variations with temperature. |
7. |
(8) LV inboard profile. Initial sizing by ∆v & specific impulse including “real-life” additions for startup, ullage, thermal contraction. Tank geometry: diameter & dome shape. Engine selection. Mass estimation. Calculation of Center of Mass and mass moments of inertia. Two-stage to orbit detailed example. |
8. |
(9) Loads: transportation (handling/road/rail/ship/plane), effective load from distributed loads, ground winds on pad, in-flight aerodynamic & inertial forces during trimmed flight at max-q. Graph of normal loads. Calculation of distribution of moments, shears, axial loads. Detailed Saturn V example. Load curve rules-of-thumb. Measuring atmospheric winds, Jimsphere. Load relief during launch. (10) Stress terminology. Cylinder analysis. Stress due to axial & bending loads. Allowable stress based on stability/buckling. 7 ways to improve stability. Internal stresses due to aero loads. Benefits of internal pressure, thermal effects. |
9. |
(10 cont.) Hydrostatic head, geysering. Overall stress state & required thickness calculation for tanks, skirts, adapters, interstage. (11) Launch environment: vibration, shock, acoustics, thermal loading. Startups, cutoffs. Explosive/ordnance & non-explosive separations. Payload fairing separation dynamics. Payload separation via clamp bands. The payload’s environment, pyro shocks. Acoustics: ignition overpressure, liftoff and max-air acoustics, acoustic suppression. Thermal environment from aero heating, plume radiation. Thermal protection systems. Spacecraft structural design verification, coupled-loads analysis. Payload isolation, acoustics, thermal. |
10. |
(12) Guidance, stability & control. Guidance & navigation vs. attitude control. Attitude determination. Stability & control: how to stabilize unstable vehicle. Flight control system elements. Thrust-vector controlled (TVC) vehicle equations of motion. Vehicle tank positioning. LV block diagrams, transfer functions. Intro to complex variables & root locus diagrams. Wind gust response. Instabilities from LV flexibility, “tail-wags-dog,” sloshing, pogo, resonant burn. |
11. |
(13) Manufacturing. Conventional & friction-stir welding. Fabrication of tanks, connecting structure. Composite layups, fabrication techniques. The future: 3D/additive printing. Stacking. (14) LV systems: propellant loading & conditioning. Pressurization systems, hydraulics, thrust-vector control. Avionics, data systems, electrical, telemetry basics. Ordnance & separation systems. Launch pad facilities: umbilicals, swing arms, propellant loading, lightning protection, vehicle hold-downs. Acoustic suppression. |
12. |
(15) Testing: ground & flight wind tunnel, structure, vibration, acoustic testing. Radio-frequency/RF & software testing. Hot gas & plume testing. Redundancy, reliability, k-out-of-n systems. (16) Failure examples & lessons learned. Most common failures, case studies. Five mistakes to look for. Flight termination systems, range safety. Best practices to avoid failures. (17) LV Financial analysis, project management, cost estimation. Design decision-making, cost engineering, cost-estimating relationships, inflation. Recommendations & Atlas V cost example. Software cost. Fallacy of “cost per pound” or “per kg”. Propellant costs. |
Instructor
Contact: Please contact Jason Cole or Customer Service if you have any questions about the course or group discounts.
Title | Credit(s) | |
---|---|---|
1 | ||
2 | ||
3 | ||
4 | ||
5 | ||
6 | ||
7 | ||
8 | ||
9 | ||
10 |